Tesla Battery Production: Overcoming Supply Chain Hurdles
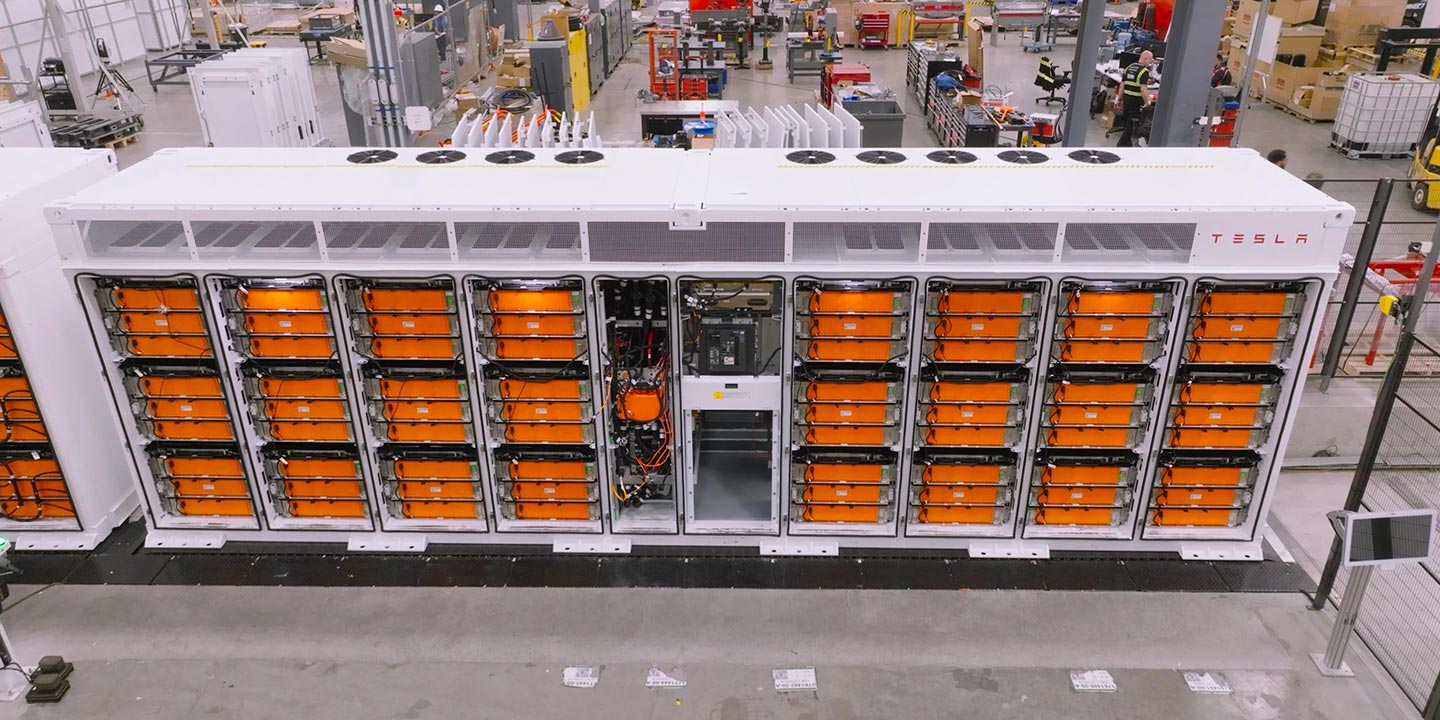
Welcome to your ultimate source for breaking news, trending updates, and in-depth stories from around the world. Whether it's politics, technology, entertainment, sports, or lifestyle, we bring you real-time updates that keep you informed and ahead of the curve.
Our team works tirelessly to ensure you never miss a moment. From the latest developments in global events to the most talked-about topics on social media, our news platform is designed to deliver accurate and timely information, all in one place.
Stay in the know and join thousands of readers who trust us for reliable, up-to-date content. Explore our expertly curated articles and dive deeper into the stories that matter to you. Visit NewsOneSMADCSTDO now and be part of the conversation. Don't miss out on the headlines that shape our world!
Table of Contents
Tesla Battery Production: Overcoming Supply Chain Hurdles
Tesla's ambitious growth targets hinge critically on its ability to secure a robust and reliable supply chain for its electric vehicle (EV) batteries. Recent years have presented significant challenges, forcing the company to navigate complex geopolitical issues, material shortages, and escalating costs. However, Tesla's proactive strategies are starting to yield results, demonstrating a commitment to overcoming these hurdles and solidifying its position as a battery technology leader.
Navigating the Complexities of Global Supply Chains
The production of lithium-ion batteries, the cornerstone of Tesla's vehicles, relies on a complex network of global suppliers. From mining critical raw materials like lithium, nickel, and cobalt to the manufacturing of battery cells and packs, each stage presents potential bottlenecks. Geopolitical instability, particularly in regions rich in these resources, has created significant uncertainty and price volatility. Tesla, like many other EV manufacturers, has had to grapple with securing stable and ethical sourcing of these essential materials.
Addressing Raw Material Shortages: A Multi-pronged Approach
Tesla's response to material shortages has been multi-faceted. The company has invested heavily in:
- Direct sourcing agreements: Establishing direct relationships with mining companies ensures a more predictable supply of raw materials, mitigating the risks associated with relying solely on intermediaries.
- Vertical integration: Tesla is increasingly involved in the entire battery production process, from raw material extraction to cell manufacturing. This strategy reduces reliance on external suppliers and allows for greater control over quality and costs. Their Gigafactories are a prime example of this vertical integration strategy.
- Technological innovation: Tesla is actively researching and developing alternative battery chemistries that rely less on critical and scarce materials like cobalt, potentially reducing their reliance on volatile supply chains. This focus on innovation is crucial for long-term sustainability.
- Recycling initiatives: The company is investing heavily in battery recycling programs to recover valuable materials from end-of-life batteries, creating a more sustainable and circular supply chain. This reduces reliance on new mining and contributes to environmental responsibility.
The Gigafactory Network: A Strategic Advantage
Tesla's network of Gigafactories plays a crucial role in mitigating supply chain risks. By strategically locating these massive production facilities closer to key markets and raw material sources, Tesla reduces transportation costs and lead times. This localized production significantly improves efficiency and reduces vulnerabilities to global disruptions.
Looking Ahead: Continued Innovation and Strategic Partnerships
While Tesla has made considerable progress in overcoming supply chain hurdles, challenges remain. The ongoing demand for EVs necessitates continuous improvement in battery production efficiency and cost reduction. Tesla's future success will depend on its ability to continue innovating, securing strategic partnerships, and fostering a resilient and sustainable supply chain. This includes ongoing investment in research and development, strategic alliances with key suppliers, and a continued focus on ethical sourcing practices. The company's commitment to vertical integration, technological advancement, and sustainable practices positions it well to navigate the evolving landscape of the EV battery market. The coming years will be crucial in determining whether these strategies will ensure Tesla maintains its competitive edge in the rapidly expanding global electric vehicle market.
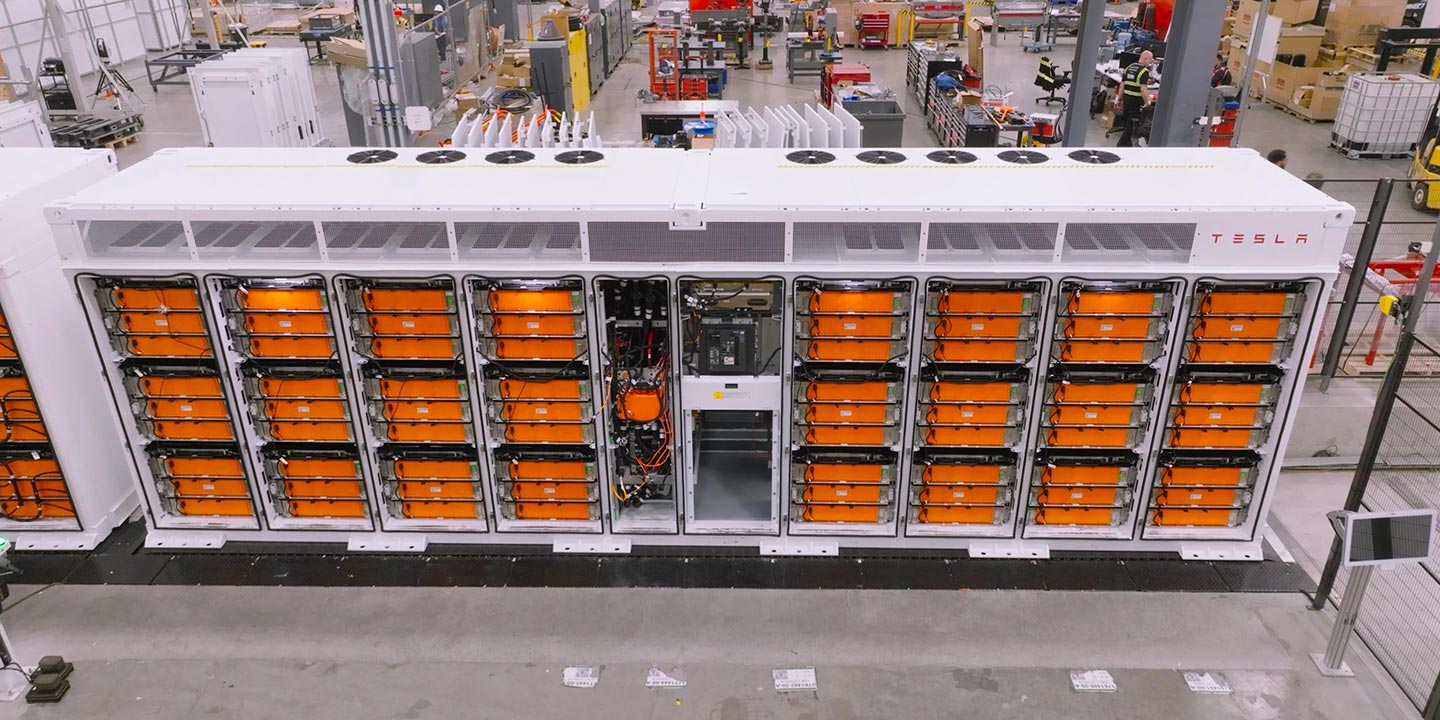
Thank you for visiting our website, your trusted source for the latest updates and in-depth coverage on Tesla Battery Production: Overcoming Supply Chain Hurdles. We're committed to keeping you informed with timely and accurate information to meet your curiosity and needs.
If you have any questions, suggestions, or feedback, we'd love to hear from you. Your insights are valuable to us and help us improve to serve you better. Feel free to reach out through our contact page.
Don't forget to bookmark our website and check back regularly for the latest headlines and trending topics. See you next time, and thank you for being part of our growing community!
Featured Posts
-
Cbse 10th And 12th Board Results 2025 Live Updates And Where To Check
May 14, 2025 -
Singapore Health Ministry Addresses Recent Increase In Covid 19 Cases
May 14, 2025 -
Bad Thoughts By Tom Segura A Critical Review Of His Netflix Stand Up
May 14, 2025 -
Quordle Hints And Answers Monday May 12th Game 1204
May 14, 2025 -
Pharmaceutical Showdown Eli Lilly And Novo Nordisk Battle For Weight Loss Supremacy
May 14, 2025
Latest Posts
-
The Power Of Trauma A Critical Look At Dcs Doom Patrol
May 14, 2025 -
Teslas 4680 Battery And Dojo Chip A Deep Dive Into Technological Innovation And Strategic Importance
May 14, 2025 -
Increased Measles Transmission Predicted For Summer Travel Months What You Need To Know
May 14, 2025 -
Sgx Delistings Accelerate Amidst Economic Uncertainty A 2024 Overview
May 14, 2025 -
Nissans Cost Cutting Measures 20 000 Job Losses Plant Closures And Post 2026 Project Freeze
May 14, 2025